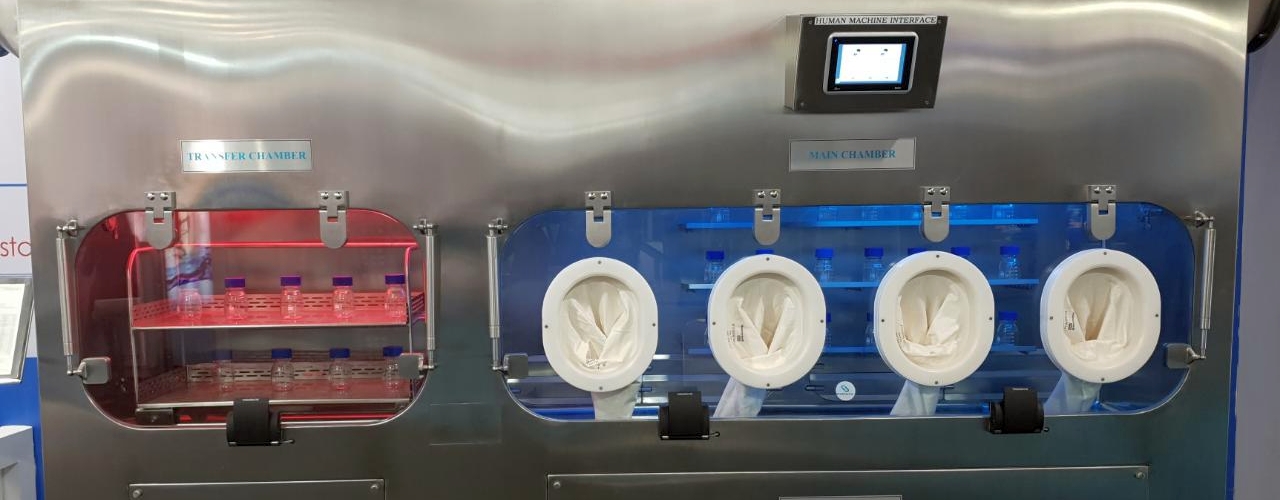
The Standard Group of Companies, incorporating Schematic Engineering Industries, are specialists at manufacturing bespoke, client specific Barrier Isolator systems to cGMP and cGAMP standards.
Positive pressure isolator systems are a key part of the Schematic Engineering Industries capabilities.
Sterility testing of sterile pharmaceutical products is required by Pharmacopoeias regulations, as to ensure the batch meets all strict guidelines and standards.
This is a critical part of validation and it must be performed, plus this also will negate the risk both false positive and false negative results.
Positive pressure barrier Isolator designs are used throughout the industry and include sterile injectable drug filling to cytotoxic sterile drug compounding.
Positive pressure barrier isolators are also essential where external contamination from either the clean-room environment or personnel in the vicinity have the capability of sterility infringement.
In simplistic terms the air pressure in the isolator is greater than that outside of it, therefore the equipment rejects possible contamination and the sterile process media is protected.
These positive barrier isolation systems provide superior sterility compared to that of open front clean air devices such as laminar flow clean benches and cabinets.