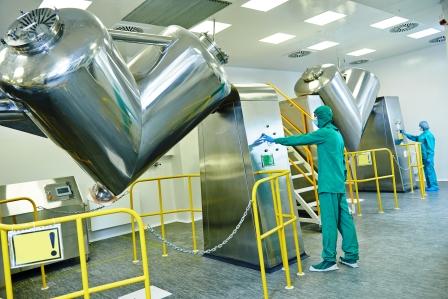
The Standard Group of Companies is a leading supplier of equipment in the pharmaceutical and chemical industry.
Part of the current portfolio is a V Blender which is manufactured by the S2 Engineering Services division, part of the Standard Group of Companies.
These blenders are designed, manufactured, installed and commissioned to standard and bespoke customer requirements.
Additionally they are called a V-Type and are also known as V-Shell, Vee Cone or Y Cone blenders.
The raw material that is placed in the blender is secured to the v-shell inlet orifice, and then both drum and V-shell are inverted by the blender through 180 degrees.
This will then allow the powder to be introduced to the V-Shell under gravity.
Diffusion blending happens when particles are distributed over a freshly developed interface, which will lead to a homogenous product.
The blenders are ideally placed for low shear tumble blending of powders and granules.
The V-Blender is essentially made of two hollow cylindrical shells joined at an angle of 75° to 90°.
The blender shell is located on pivots to allow it to rotate, and as the V-blender tumbles the material continuously splits and recombines, with the mixing occurring as the material falls randomly inside the vessel.
The repetitive converging motion of material, friction and straight sides results in a best practice and homogenous blend which has been supported by a diffusion process.
For more information click here or contact the UK or Indian offices.