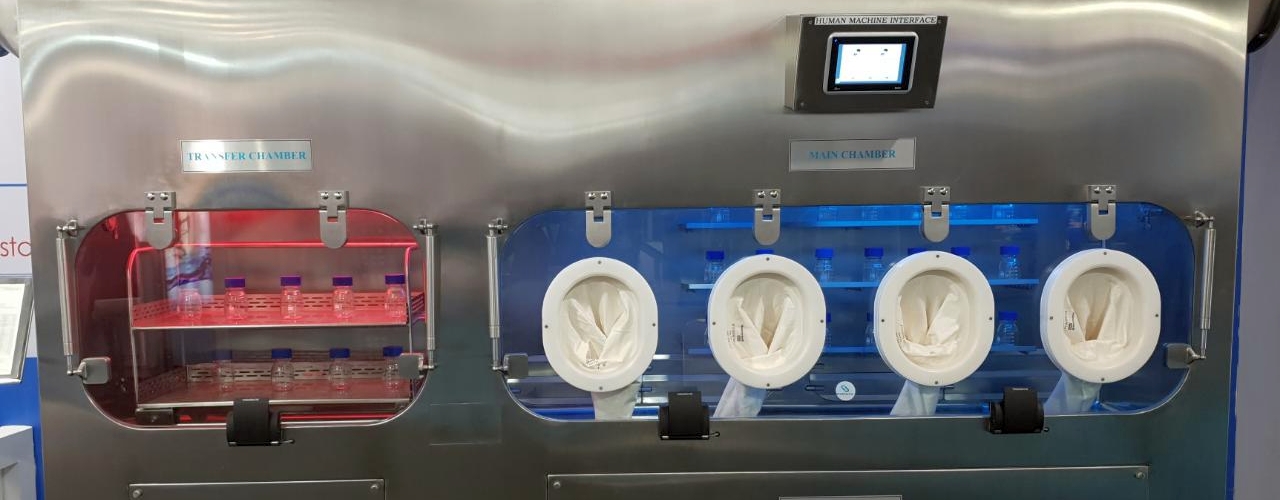
The Standard Group of Companies is a leading supplier of equipment into many vibrant and buoyant industries.
Many of these industries use acronyms, and the simple primary reason abbreviations are used is convenience.
Other reasons acronyms are used is to make reading easier, and to avoid unnecessary errors, especially when pharmaceuticals are being manufactured.
2 key acronyms that are used, and relate to equipment produced by the Standard Group is CIP and SIP.
Industrial sectors benefit immensely from using CIP processes.
This is because a cleaning method that has been created, enables the internal surfaces of sealed systems to be cleaned, and without the need for disassembly.
Process efficiency depends on the effective cleaning of all equipment on an agreed schedule during manufacturing.
Clean-in-Place (CIP) systems can be incorporated into all the equipment used by the pharmaceutical industry, including both solid and liquid dosage formulation systems.
For the most part, the CIP process is an entirely automatic one that complies with defined process times and parameters.
The cleaning operation is performed in a series of defined steps that have usually been agreed in the design stage of the project and is totally dependent on the application.
The Standard Group of Companies offer many types of equipment into these industries, on small and large scale and include the design, manufacture, installation, and commissioning.
Standard design and customer specific requirements are provided to the highest quality anf fully comply with cGMP regulations and procedures.
Steam-in-place (SIP) sterilization is an essential process, primarily in the biotechnology industry.
The SIP process is an extension of the CIP process by additional sterilisation, without any necessity for disassembling the plant and the measuring equipment.
The sterilisation of hygiene-critical processes takes place at the end of the actual CIP process.
The Standard Group of Companies manufacture flexible and rigid barrier isolators, with both positive and negative pressure.
These barrier isolators not only prevent contamination and protect the operators, but they also ensure CIP and SIP procedures are in place throughout the whole process.
OEL levels of 1 to 5 can be accommodated and cGAMP alarms and safety measures are added in case of any breach.
Please click here for more details or contact our UK and Indian offices directly.