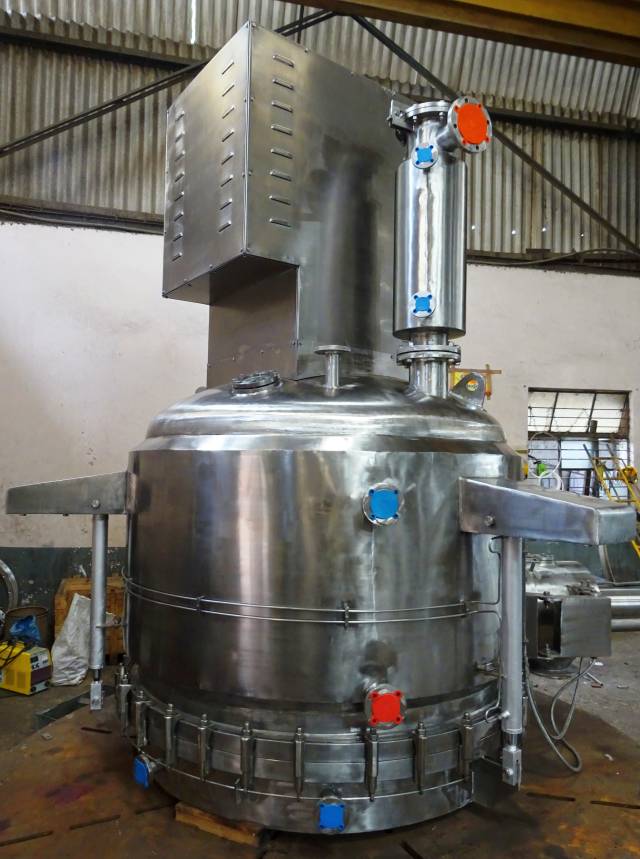
The Standard Group of Companies is a specialist at manufacturing process equipment for the chemical and pharmaceutical industry such as Agitated Nutsche Filter Dryers also known as ANFD's.
In addition, part of the Group called Schematic Engineering Industries, design, manufacture and install bespoke, client specific Barrier Isolator systems including agitated nutsche filter dryer (ANFD) Discharge Barrier Isolators to cGMP and cGAMP standards.
The agitated nutsche filter/dryer is a multipurpose piece of equipment.
The primary role is separating and then isolating solids from a solvent.
Historically this was done by 2 or more machines but with innovation this stand-alone machine does all operations which give huge advantages to the manufacturer.
The closed system now allows tight control parameters that are critical in the process which include: -
During the ANFD filtration process, filtration occurs under vacuum or pressure in the closed vessel.
After filtration, the processed media is dried into a “cake” substance.
The entire vessel is kept at the correct temperature by using a heating jacket through which heat transfer media can flow.
Additionally, these units protect the operators from all toxic substances as well as protecting the product from the atmosphere.
After the mixing and filtration processes are complete the “cake” is formed and can be classed as a slurry.
This “cake” can be discharged at this point or can be dried as a final process and subsequently discharged as a powder.
When using an ANFD, a paddle is used to mix the ingredients in the sealed unit.
When the process is complete and the product has been ejected,there is a gap of approx 15mm between the filter at the bottom of the machine and the paddle idling point.
This “cake” cannot be ejected into the discharge port for further processing.
This “cake” is expensive and is washed away in the cleaning process as not to contaminate the next production batch.
With an attached ANFD Discharge Isolator the operator can remove the “cake” safely which would otherwise by lost.
The cake at this point is usually one or both of the following: -
The operator will scrape “cake” from the base of the ANFD filter and place into the discharge point. This will then increase the yield of the batch.
Some “cakes” are extremely expensive so there is a cost which needs consideration.
The recovering of this “cake”, not only is this a commercial issue for the plant, it is invariably a quality issue.
Left over “cake” creates cross contamination risk/potential for the next batch.
Therefore, a Discharge Isolator whilst using and ANFD is critical from a health and safety point of view with the added benefit of commercial awareness.
In summary – Benefits of a Discharge isolator when using an ANFD
The Standard Group of Companies will design, manufacture, install and commission Discharge Isolators to existing machines or provide the turnkey packages for relevant and suitable processes.