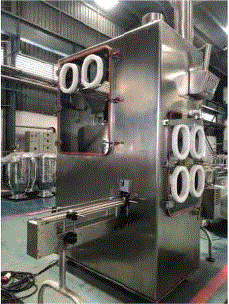
The Standard Group of Companies is a leading provider of equipment into the pharmaceutical industry.
Filling machines and the need for Isolators are getting more popular by the day due to increased demand and new advances in science.
Such advances is why Pharmaceutical engineers currently face many challenges every day.
The challenges include:
This is crucial in the interaction between the bottle filling machine, the barrier isolator system and subsequent machines in the process.
The Standard Group of Companies manufacture bespoke barrier isolators and equipment solutions which can offer full liquid and powder filling systems.
These barrier isolators can also integrate with customer filling machines and conveyor systems which will then significantly reduce the risk presented by direct human intervention.
From complete filling lines to stand alone aseptic processes they all adhere to regulatory standards and cGMP guidelines.
These isolators provide an aseptic environment achieving ISO 5 grade A classification and allow for the entry of pre-sterilized products entrance through an RTP (Rapid Transfer Port). This can be either the cap, stopper or even the powder.
The vials are then automatically moved by the filling machine through the stations and exit the isolator at the opposite side.
Not only does the isolator provide and maintain an Aseptic environment, it also allows human intervention from the glove ports which allow manipulation and hence increase productivity.